Mold
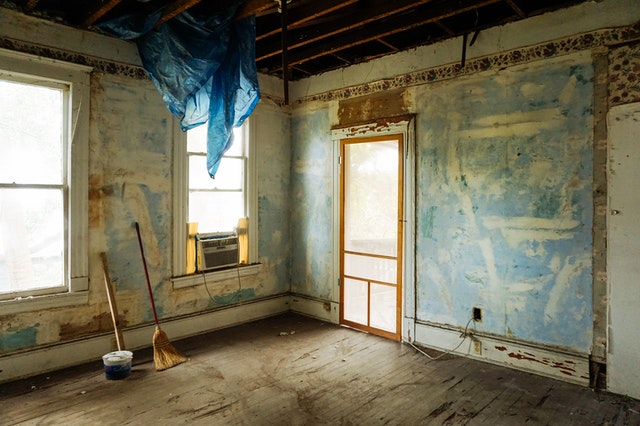
Mold This is an excerpt from the Book called “Estimating Rehab costs” by J Scott . Continue reading to learn more about Mold, thanks to the author. Mold Overview For many investors, mold is the most terrifying renovation issue they’ll ever face. Hopefully, after reading this section, that won’t be the case anymore. Mold is a fungus that occurs naturally in the environment, mostly in soil and on dead or decaying organisms. In fact, if you were to do a mold test outdoors, you’d find that the mold spore count is pretty high. But you don’t generally worry about encountering mold outside, do you? Mold only becomes a problem when it starts to grow in exceptionally large quantities indoors, or when certain types of dangerous mold spores start to grow. In order to grow, mold need two things; moisture and a food source such as wood, insulation, sheetrock, or cloth. If you take away either the moisture source or the food source, mold will stop growing. When you have mold growing in a house, the remediation course involves three steps; Common moisture sources are leaks (for example, in a roof, a water heater, a toilet) or high humidity from a house being unoccupied and closed up for a long time. Once the moisture source is removed-the leak fixed or the humidity problem resolved—the mold will stop growing. At that point, once the existing mold is removed—for example, by removing any moldy sheetrock, flooring, or cabinets—the problem is resolved. An air quality test (AQT) can tell you the count and type of mold spores once you’ll know if the problem has been adequately resolved; and once you confirm the mold has gone through a third-party mold test, you can put the house back together. only an AQT cab tell you for certain if your house has mold and what type of mold, but if you see mold in a house, that’s a pretty reliable indicator. Some people believe that if you smell mold, there is a big problem. In reality, many distressed houses haven’t been lived in for long periods of time, and it’s pretty common for these closed up houses to smell musty without there being a major mold issue. In many cases, opening up the windows for a couple days or getting the air conditioning running again with take care of the smell, and an AQT will indicate that there are no remaining mold issues. That said, if there is a mold problem, the first course of action is going to be to determine the source of moisture and get it remediated. This should be done prior to bringing in a mold remediator, as remediating the mold won’t be a long-term fix if the moisture problem isn’t resolved—the mold will just grow back. At any time in the process, you have the option to bring in a testing company. But if you’re fairly certain that there is a mold problem, the testing will only confirm what you already know. Save your money, do the remediation, and then do the testing at the end to confirm that the remediation worked. Regardless of what anyone tells you, mold remediation of any area larger than ten square feet is not a DIY project. Instead, you’ll want to bring in a qualified mold remediator. Different states have different requirements for licensing mold remediators—in some states, you need to be licensed to legally remediate mold problems; in other states, there are no requirements whatsoever, so finding a qualified remediator can be a bit more difficult. Once the remediator evaluates the problem, it’s very likely he’ll recommend removing any porous building materials that have been impacted by the mold. This might include wet sheetrock, wet carpet and pad, and moldy cabinets. While you may be able to do this demo yourself, some areas have very strict biohazard rules around disposing of moldy material. Ask your mold remediator if you can do the demo yourself or if he recommends doing it himself. I look at mold problems just like I look at roof issues , cracked windows, or dirty carpet—it’s going to require bringing in a knowledgeable contractor or two, paying some money, and getting the work done. While it may be more expensive and time consuming than those other fixes, ultimately, it’s no more complicated or daunting. I don’t let mold stop me from buying a house at the appropriate price discount, and neither should you. Just note that, in some states, you will be required to disclose the mold to future buyers; if you had the work done by a reputable contractor, you should also have a warranty that will ease the buyer’s minds and you’ll hopefully find that resale isn’t any more difficult than if the mold were never there. Inspection Tips There are several way to do a cursory mold inspection in a property that you’re walking through, but the most basic—and often the most accurate-is to simply use the sniff test. Mold tends to have a very distinctive rate—is to simply use the sniff test mold tends to have a very distinctive smell, and after you’ve smelled it once, you’re unlikely to forget it. Keep in mind that a musty smell isn’t always indicative of mold—houses that have been closed up for long periods of time without much airflow will often have a stale odor. It’s common for foreclosed homes. Or homes where the electricity is turned off, to have a strong smell of stale air and mustiness. If you come across this in the property you’re inspecting, don’t be alarmed—but definitely take note and do some additional investigation and due diligence to determine if mold is the issue or not. In addition to smelling for mold, you should be on the lookout for mold on walls, in closets and especially in any place where there is a risk of water intrusion or leaks. When I inspect a property, I always carry a flashlight, and do a detailed search of all parts of the basement, attic, and garage—there places
How to soundproof a room cheaply? Easy and Affordable Methods to Soundproof a Room
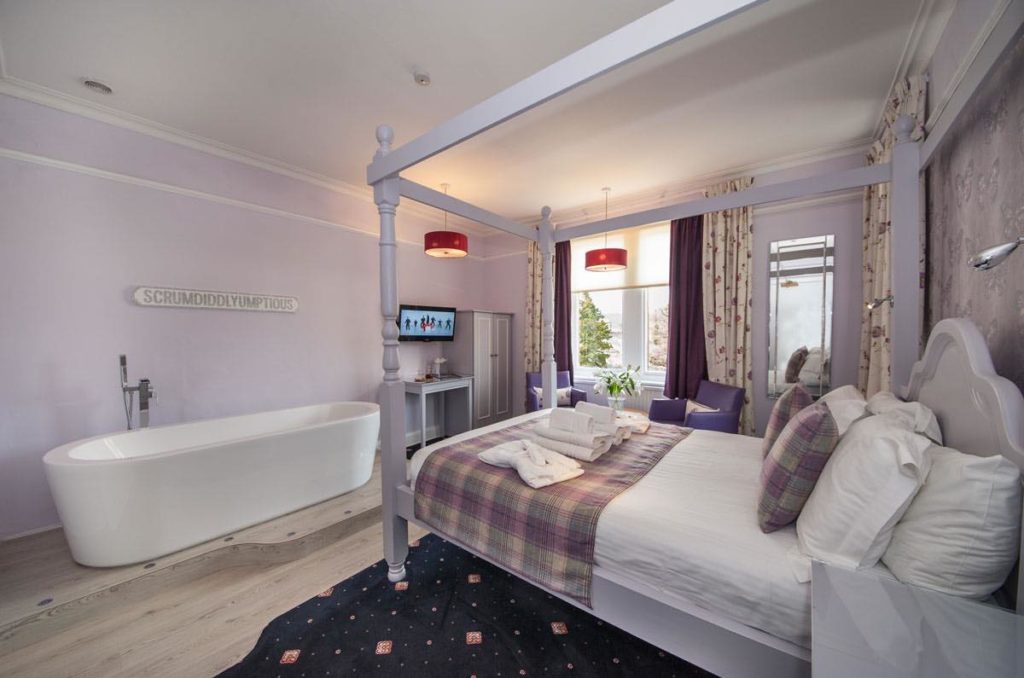
How to soundproof a room cheaply? Easy and Affordable Methods to Soundproof a Room For many of us, home is where we relax, escape from the outside world, and experience moments of blissful peace. But all too often, our fortresses of solitude are invaded by the sounds of traffic, neighbors, pedestrians, and construction, seeking to disturb us and jolt our minds out of their restfulness. Our home should serve as a quiet, peaceful recipe from the hustle and bustle of the outside world, but that is becoming increasingly more difficult as the world gets busier and noisier every day, especially if you are still working from home and need some solitude to get anything done to silence the record you can effectively soundproof rooms to dampen the tin of traffic sirens, airplanes, honking horns and other noisy intrusions going on in and around your home especially if you are not a fan of wearing noise-canceling headphones all time. Headphones may be a symptom of modern life, but that does not mean we have to put up with it. This article will explore how to soundproof your house and restore the Zen of a peaceful home. The Cheapest Way to Soundproof a Room. The first thing to do is plug up all of the weak sound leaks in the room, typically the door and the window. Now to plug up a window, you need a window plug. And a window plug is, might be a sheet of sheetrock, cut out to fit into the window frame, and you just maybe put a couple of handles on it and plug it into the window. Now you’ve eliminated the sound in the room from getting out the window. Now sometimes you want to soundproof within the house, and there’s a door. Now to sound, the best- The first thing you have to do to soundproof a door is to eliminate all the air leaks. So go to the home improvement store, get a weatherstripping kit, open the door, install the door for six dollars this little foam strip, and install it around the door. Buy the proper thickness kit, so you might measure the gap between the door sill and the door, close it and measure it. Because you want a compression fit, it doesn’t do you any good to put a foam strip around the door and then have an 8th of an inch gap between the door and the front beginning of the foam strip, that’s not a compression seal, it needs to seal airtight all the way around. And then, on the floor, you need some wiper. Again, at the home improvement stores, you can find these metal strips with a felt wiper attached to the bottom with some screw holes; buy two of them. Put one on one side of the door, snug up against the floor, and the other on the other side of the door, snug up against the floor, so you’ve got a double wiper that you drag across the floor. Even if it’s carpet, still put a double wiper. Anyway, that’s the quickest way to improve soundproofing a room in the house significantly. Have been searching for easiest and the cheapest methods to sound proof your room/house? Most methods that you have come across are probably insufficient for the deadening sound of your room. If you want to properly soundproof a room from noisy neighbors, traffic, etc., you would have to add mass, decoupling, damping, and absorption, which can prove to be costly. For reducing the noise in the room, you will have to soundproof the walls, ceiling, doors, and windows. Cheap soundproofing techniques will only help a bit. But they are much better than doing nothing at all. With these DIY methods to soundproof a room of an apartment or house on the cheap, you will be on the right track. Door weather stripping Interior doors don’t typically have weather stripping, but adding some around the perimeter of the doorway can help muffle sounds. Peel and stick from rubber weatherstripping from a very tight seal are affordable and easy to install. It is one of the oldest types of weather stripping. It comes in those with or without adhesive backing and is very affordable and surprisingly effective in blocking noise. You can also install a doorstep or under-door draft stopper to the bottom of the door to seal off the gap along the floor. Wall hangings Hard surfaces like drywall plaster and tile reflect and amplify sounds. So, it only makes sense that soft surfaces absorb sound, making the room much quieter. Cover walls with thick blankets moving pads, tapestries, or quilts. Virtually any soft material will work though thicker ones absorb more sound than thinner materials. If you don’t mind adding an industrial look to the room, pass on sound-absorbing panels to the walls and, if necessary, the ceiling. The panels are made from superior noise dampening materials such as soft foam rubber, dense polystyrene fiber, and cork. Rocks Sound does not only bounce off the wall. It can be refracted by hard floors too. If your room has a hard surface floor wood tile or laminates, the simplest solution is to lay down an area wrap to help absorb noise. And again, thick cracks are better than thin ones. Also, buy an extra thick bed under the rack for additional sound protection. Absorbed vibrations Noise is transmitted through vibrations. So, any booming piece of machinery or equipment produces vibrations that can transfer noise to adjacent rooms. The equipment such as speakers, appliances, stationary bikes, and treadmills. To dampen the vibrations and quiet the room set the item on a thick piece of dense foam rubber such as a home gym floor mat or horse stall mat. Window treatments Windows, even high-end windows, are not very effective at blocking out noise, and the older the window, the worse it is at keeping rooms quiet. The easiest way to dampen window noise is
Installing Wallboard
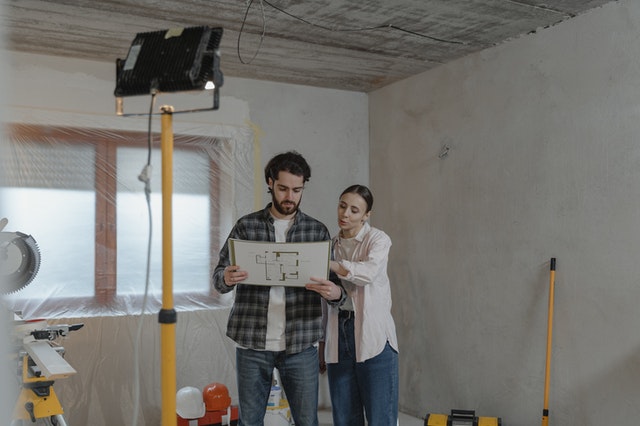
Installing Wallboard This is an excerpt from the Book called “Carpentry “ by Des Moines, Iowa. Continue reading to learn more about Installing Wallboard, thanks to the author. Thank goodness for wallboard, which makes it possible for a do-it-yourselfer to finish walls without spending a year or so learning how to plaster. But it’s still dusty, difficult, sweaty work, involving heavy lifting in awkward positions. Planning The Job Though hanging the sheets is heavy work, taping takes much more time. Gaps are difficult to tape, so take the extra time to cut accurately and to position the sheets tightly together. Hang the ceiling sheets first, then the wall sheets. A rented wallboard jack (or hoist), will make the work easier and the seams tighter. It raises sheets, allowing you to position them carefully. Using 10-foot or even 12-foot sheets is worth the extra trouble if you can avoid butt joints, which are the most difficult joints to tape. Use ½ inch wallboard for the ceiling. Consider using ⅝-inch sheets for the walls. It’s harder to lift so you may need jamb extensions, but the wall will be significantly more solid. New Construction: Inspect the framing to make sure you will have nailing surfaces for the ends of all your sheets. You may need to add nailers at inside corners. If only half a stud’s thickness is available for nailing in a corner, plan to install against that stud first if you nail to the adjoining wall first, you will lose ½ inch of your nailing surface. Over Old Walls: If your plaster walls and ceiling are cracked and spongy, you can “skin over” them with ½–inch wallboard on the ceiling ¼-inch wallboard on the walls. (If you use ¼-inch wallboard on the ceiling, it may eventually sag.) To skin over walls, you will need to remove all moldings; butting the wallboard up to molding is difficult and produces a sloppy appearance. Before you replace the moldings, cut baseboard pieces and provide jamb extensions for the casing. Another option is to remove only the moldings and plaster, leaving the lath in place. Depending on the thickness of the plaster, install ⅜-inch or ½-inch wallboard. Removing plaster is messy and difficult, but the finished wall will be very strong and you won’t have to modify moldings. When skinning over or attaching to lath, sheet ends do not have meet on centers of studs or joist edges; attach them to the lath with screws ( not nails), and apply adhesive. Measuring And Cutting Few things are more frustrating than missing a stud or joist while struggling to hold a heavy piece of wallboard. Take a minute or two to mark locations on the sheets. If you framing members are 16 inches apart, use a wallboard square (which has crosspieces 16 inches long on one side) to quickly make a series of pencil lines. When cutting wallboard to length, cut the wallboard ¼ inch shorter than the measurement calls for; this compensates for the somewhat ragged edge of the cut. To make a square crosscut, make only one measurement mark. Hold the drywall square in place with your foot against the bottom, and score through the paper. Bend the cut piece back, and cut through the paper on the other side. For a rip cut parallel to the edge of a sheet, use the drywall square to measure and as a guide (above right). For rip cuts not parallel to edge, measure each end and chalk, a line between; cut freehand. Make cutouts for electrical boxes ¼ inch larger than the boxes. With a tape measure or drywall square, mark the two dimensions in one direction, and then in the other direction, and draw a rectangle. Cut out the opening with a drywall saw or a knife (right). To cut circles for pipes, measure to the center of the hole only, and use a circle cutter. Cut on both sides, and bang the hole out. Vertical Or Horizontal? Installing sheets with the tapered joints running up and down will mean that you avoid butt joints, which are very bothersome. However, it can be difficult to line up the edges so that they meet at the center of a stud (or “splitting the stud”) all along their length. Running the sheets horizontally may require butt joints, but it will be easier to split on studs. And, the horizontal tapered joints will be easier to tape than vertical joints running from floor to ceiling. Installing Wallboard Hanging The Sheets Wallboard sheets have tapered edges along their sides. When a tapered edge is butted against a tapered edge, the resulting joint is easy to tape and will not bulge out. When sheets are butted end to end, however, that joint will take time and will never be truly straight. So don’t economize by using cut pieces of wallboard if it results in more butt joints. The material is cheap, after all. Correct Fastening: A fastener’s head must be driven below the face of the sheet, but not so far that it breaks the paper. Even a slightly protruding head is impossible to smooth over. And, if the paper is broken, a fastener is nearly useless. Use a drywall hammer for nails. It is light and has a wider head that makes it easy to dimple the nails without harming the paper. Use a wallboard shooter to fasten screws. It’s a drill that you can adjust to the depth you want. Or, buy a dimpling but, which you can put on a regular drill and is nearly as effective. Fasteners that do not grab wood will work themselves out in time. If you miss a stud or joist completely, remove the fastener and try again. If the fastener barely catches the side of the stud, angle-drive another fastener next to it and directly into the wood, to hold the first one in place. Building codes have varying regulations concerning how many fasteners to use. To be safe, space nails or screws 7 inches apart on the ceiling and 8 inches apart on
Making The Mold Edges
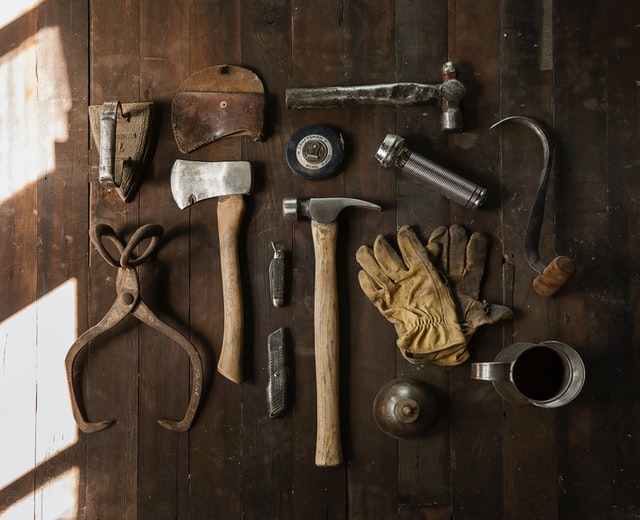
Making The Mold Edges This is an excerpt from the Book called “Making Concrete Countertops. Continue reading to learn more about Making The Mold Edges, thanks to the author. Because the countertop will be 1-3/4” thick, rip 1-3/4” mold walls from 3/4″ melamine on the table saw. Countersink screw holes into the edges of the mold walls. We will use 2-1/2” screws so that they will go through the 1-3/4” mold edge and into the base of the mold, but not through. And steel Straight-edge helps align the sizing or thick wall of the mold. Measure the side walls and run. On the bold saw level the front edge of the sidewall to match the angle of the curved stripe. Screw the sidewall of the mold and piece. Cut out blocks from 3.4” melamine 1-3.4” wide. These blocks will support the curved wall in the mold. Countersink screw holesin these bracing blocks for the radius edge. The curved wall is made of 1/4” melamine, ripped to 1-3/4”. Cut a strip long enough to form the curved wall, allowing a couple of excess inches on each side. Affix two blocks, one to each of the beveled sidewall molds. Bend the 1/4” melamine strip to the radius line drawn earlier. Fix one block to the centerline. (Note that the radius edge pencil line should show on the inside edge of the 1/4” melamine strip). Now affix the rest of the blocks, evenly spaced and placed so that the melamine strip can be attached just outside the drawn radius edge line. Use finishing nails to affix the 1/4“melamine strip to the blocks behind it. The nails are so small that we won’t need to use Bondo. Fit the sink mold into placer. Use a pencil to mark places where the sink doesn’t fit properly against the raised drainboard. A little bit of dried resin and wood needs to be carved away with a knife where the fit is too tight. Drive two screws through the base of the mold on either side of the centerline and remove them. The holes will work as a guide when securing the sink mold from beneath. Turn the mold upside-down on the worktable, so that the sink mold can be accessed from underneath. Screw the sink mold to the base. Use 100-grit sand paper to smooth the mold. Take time to really go over it and make sure it’s perfect. Creating A Faucet Knockout We Need To Make holes for our plumbing. Once you know which faucet you will be using, you are ready to proceed with making the displacement for the holes. Although you can drill them later, it’s preferable to cast them into your mold. Using an architectural circle template, trace a 1-1/2“circle on 1-7/8” foam. Mark the center. Cut out a cylinder using a bendsaw. Hold the cylinder next to the mold wall to test for height. This foam piece is a little too tall. Use course sand paper to reduce the height of the cylinder until it is flush with the mold wall. Use the corner of the mold to ensure a level, perfect finish when sanding. Wrap the foam cylinder with vinyl tape. Trim the tape with a knife. Measure and mark the knockout position on the mold. Create a starter hole in the melamine base of the mold using a screw. Drive a screw through the center of the knockout cylinder. Use the starter hole to align the screw and affix the knockout. Affix drain knockout to center of sink mold. We are using a rubber mold manufactured by Buddy Rhodes Studio.
Concrete Plates
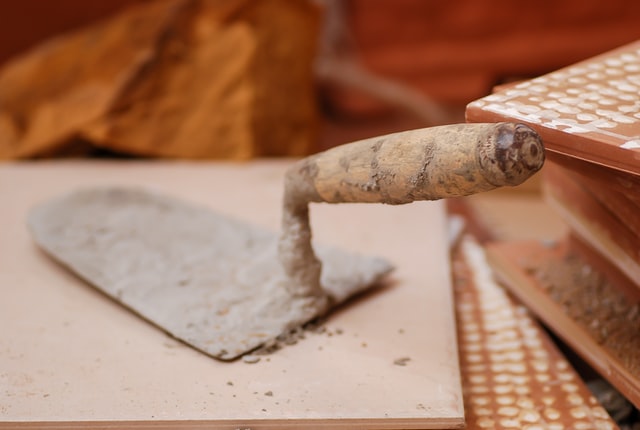
This is an excerpt from the Book called “Concrete 43 DIY projects for home & garden” by Malena Skote . Continue reading to learn more about Concrete Plates, thanks to the author. Plates Sisters Ann and Louise Turlock have been casting concrete in their spare time for a number of years. They now specialize in casting concrete plates from the tops of old silver-plated plates. The concrete plates become copies of the metal plates, with patterned borders and filigree. Ann and Louise don’t use oil or any other release agent, but place the concrete directly on the tray’s back. They then glaze the finished concrete surface white, and the result is slender, almost ceramic-like plates. There are plenty of old silver-plated plates and gold-plated trays available at flea markets and second-hand stores. Study how the back of the tray looks, as it is this side that will create the impression in the cement. Check also that the edge isn’t curled back as this can cause the tray to get stuck in the concrete. The tray should be somewhat flexible so that it’s easy to extract from the concrete. You can make the plates quite thin, but you must be as careful with them as you would be with ceramic plates. Concrete Plate Cast On A Silver Plate Mold Silver plate with ornamental border Materials Fine concrete White, water-based paint Small furniture pads Tools Mixing pail Trowel Metal spatula Plastic sheet File Thin, tapered metal knife Paintbrush Rag Instructions Glazing tips Mold Round wooden plate or tray with smooth back (if the wood seems absorbent, seal it before use) Materials Wood or craft sealer (if needed) Fine concrete White, water-based paint Small furniture pads Tools Marking pen Mixing pail Trowel Spatula Plastic sheet Thin metal knife Paintbrush Instructions A shimmering fish in mirror mosaic adorns this little plate, which was cast using a round, plastic plate. The concrete was colored dark-gray using oxide black pigment. Mold Round plastic plate Materials Broken mirror Double-sided tape Fine concrete Oxide black pigment (optional) Tools Rag or newspaper Hammer Mosaic cutters Scissors Mixing pail Trowel Plastic sheet Metal spatula or thin knife Coarse sandpaper Instruction
Converting a Window to a Door
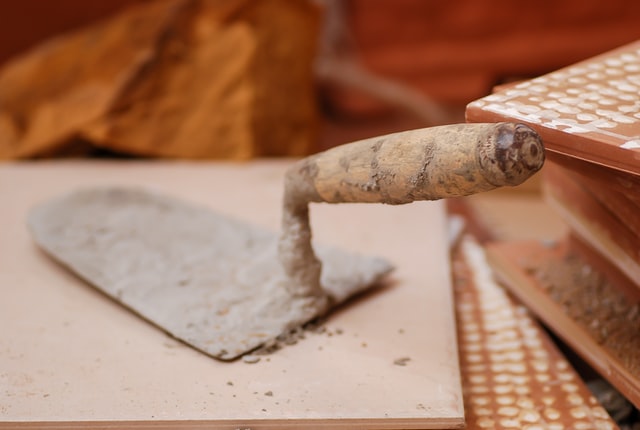
Converting a Window to a Door This is an excerpt from the Book called “Home Repair and Improvement Series“ by Bob Vila. Continue reading to learn more about Converting a Window to a Door, thanks to the author. The Trick of Converting a Window to a Door Adding anew exterior door or window to your house is easier than it sounds. Even making a hole in the all can be fairly simple if the exterior is wood, aluminium or stucco. Cutting through masonry is heavier work. Both the door and the window units come ready-assem-bled in a wide variety of styles and sizes. The quickest way to add anew door to a frame house—one whose basic structure is made of wood studs, not of solid masonry—is to take out an existing window, lengthen the opening and put a door unit in its place. To take advantage of this simple method, you must be able to find for your door opening a window of suitable size; most ready-made doors are 6 feet 8 inches high and 32 or 36 inches wide. In-side the window casing, measure the height form the underside of the top jamb to the floor and the width between the side jambs. You also need a window with no obstructions hidden in the wall beneath it; check rooms above and below for piping or cables. You may have to cut a hole and inspect the area. Where you do not have a window of the appropriate size in the appropriate place—or if you wish to put in a window, not a door—you can do that, too, by making a new opening in the wall and framing it as shown. For a flush fit outside and inside with wood, aluminium or stucco, choose a door frame4 5/8 inches thick of your interior walls are wallboard, 5 3/8 inches thick of they are plaster. For brick venner or solid masonry, either thickness will serve because the door will be recessed flush with the interior wall. Like prehung interior doors, the exterior models can be hinged on the right of log side. Unlike them however, exterior door do not have alit jamb with finished caning on both sides but come with a sold jamb that is trimmed only on the outside. You must assemble the interior trim also you install the unit. On most doors, the exterior casing or brick mould is 2 inches wide and extends about 1 ½ inches beyond the jamb. When you are replacing a window worth a door, you may need to order wider casing to make in match the size of existing exterior trim. Getting At The Window. Before you can take the basic frame, or jamb, of a window out of a wall you have to remove the rime and sashes prices by piece. The first pieces to remove are the strips of interior casing around the window and the stop moldings along the sides—and, sometimes, the top—to the jamb. Then comes the apron under the interior still, or stool, and the sill piece itself. Next is the hardware the holds the lazed sashes. On the standard double-hung window, shown separated from the trim in the drawing at left this hardware consists of metal channels and springs. You need to take off the exterior cases to remove them completely. Other types of with downs have sash cords or hinges. You can life out the sashes from the inside and remove the exterior casing afterward; a little experiment will show what you need to undo. Removing The Window Preparing The New Opening Repeat the procedure on the other side of the window. Using the utility bar if necessary, pry off the wall-finishing material between the cuts. Now the inside of the wall will be exposed so you can see the existing framing. For wood, aluminium or stucco siding set the blade of a circular saw a carborundum blade for stucco—to the maximum depth of the siding. Plug the saw into a GFCI-protected outlet remove any nails in the cutting line and cut along the lines, but avoid sawing into the sheathing; the border of sheathing left around the window opening will be continued for the door opening. Pry off siding between the cuts. For brick siding, score the bricks along the drawn lines and remove the bricks inside the lines Fitting And Finishing An Exterior Door Push the frame backward and forward in the opening until it is plumb; if necessary, insert shims at the back of the top casing. Drive nails partway into the side jambs about a foot below the top corners, then hang the door on its hinges and follow the directions to shim the door from the inside. Pack strips of fiberglass insulating material around the top and side jambs of the door.
How Much Does A pre drywall inspection cost
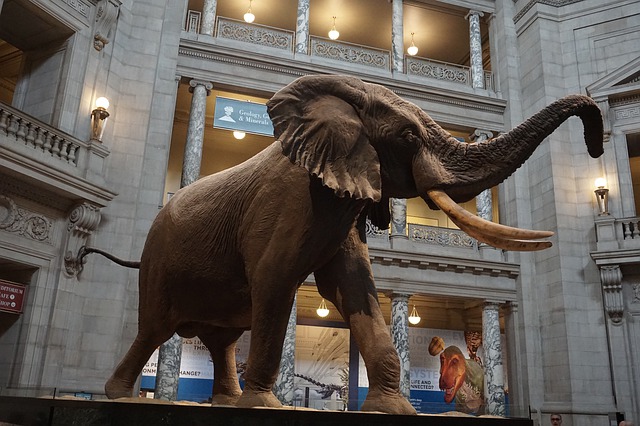
How Much Does A Pre-Drywall Inspection Cost? Important Things to Know Before Going For Pre-Dywall Inspection There are many details to be considered throughout the construction process. In addition to the various rules and regulations that preside over construction in your local area, there are other details like the pre drywall inspection to consider as well. All in all, dealing with the repair hole in drywall construction project can be a frustrating ordeal. The best way to avoid the frustration of this project is to remain as informed as possible. Arming yourself with all the information about your projects is the best way to avoid unpleasant surprises that tend to crop up along the way. To this end, we have compiled a short compendium of information, so that you can know exactly what to expect and make sure that nothing is overlooked. An inspection of the major systems of your home at the pre drywall stage includes: Structural framingFoundationRoofExterior grade,Electrical layoutPlumbingThe time it takes to complete this inspection can range from 1 to hours and depends on the size of the property being inspected as well as any specific issues the client is interested in. Any specific issues may require additional pictures and documentation, as we will see in the article below. Complete peace of mind … from $100 to $250! Of course, this is not a required part of the project. Nevertheless, there are plenty of reasons that it would be a good idea for you to invest in this inspection. You will be provided with a detailed report on all the issues your project manager finds in their inspection. This saves you from having to do this important inspection yourself and provides a professional perspective that most of the population simply lacks. Most often these inspections are concluded with a report that declares the complete absence of anomalies. But when an issue is found, it is never a small issue. I have seen potential drainage issues, joists that have been accidentally cut, and many other issues that can be expected to cause considerable issues further down the line. Furthermore, if your inspector does uncover an issue, sometimes it is an issue that is already being fixed and can therefore fall into your new home warranty. Documents The first and most important part of the inspection will be plenty of photos and footage. Think about all the issues that can be solved by a clear picture of what is happening behind the scenes in your own house. Will you want to hang wall art in the future? Then you will want to know what is behind the wall you plan on hanging your art. You will probably want to do some renovations at some point, you will be very happy to have this clear documentation and photo evidence of what you can expect to find hidden in the walls. I would recommend going all out and having a 3D Matterport model of your home created as well. This will allow you to spend more time on the inspection itself and less time on taking the picture and making videos. Furthermore, the 3D rendering of your home will make it far easier to plan future projects than thumbing through 1000+ pictures and 2 hours of video footage. Finally, many people love to share these 3d models with friends and family so everyone can see how things are progressing in your home. In the Pre Drywall Walk, you and your construction manager will tour the grounds of your home. This is to get acquainted with the plumbing, electrical wiring, internal systems, and any other systems or upgrades you have selected at the time you signed the building contract or have petitioned since then. Best Tips for Your Pre-Drywall Walk If you are having your home built, the best time to conduct this important pre drywall inspection is right before the dry walls go up. This way the power outlets, framing, electrical wiring, HVAC, A/V lines, and all other installations and upgrades you have selected will be installed at this point. The more questions you ask, the better! When you buy a home on resale, there is very little that you know about the construction stage of the home. As a responsible homebuyer, you already had the inspector inspect the home pre-closing, but these inspectors are limited to the things they can see. Inspectors are not there to poke holes in the walls and explore anything beyond what is readily visible. Now compare this to building a new home. Regardless of how professional the builder of the home was, there is still much to learn about what is inside your new home. This walk is your chance to get a crash course on home construction. I have attended a good many pre drywall inspections and have been utterly amazed by what I have found within. There is always much to learn about plumbing cleanouts, ductwork, air registers, flashing, electrical panels, and more. Check Your HVAC Units HVAC Units — are perhaps one of the most important functional aspects of keeping the home comfortable on the inside. Because the HVAC plays such an important role in keeping the air temperature and quality of the home on point, the HVAC and the entire ducts system are worth inspecting completely. There are several important issues you will want to keep an eye out for. Including: Gas pipe leaks Too many units near each other AC inconsistent in various parts of the home Vents not completely sealed into the walls or cabinets Venting angled incorrectly or blocked Insulation issues What this means is that performing a thorough inspection of the home’s HVAC units and the system will ensure a safer home and more comfortable home life. Plumbing System Another very important part of your drywall inspection is the plumbing system. While it doesn’t always get the praise and consideration it is due, the entire operations of the home will be brought to a