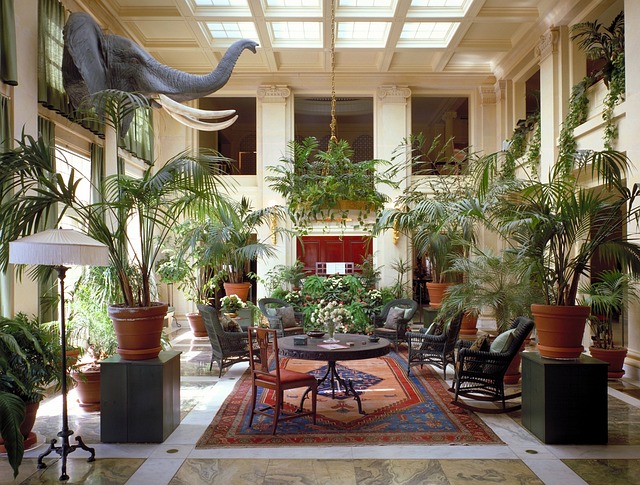
Preventing Drywall Damage: What Every Homeowner Should Know Skyline Drywall Repair Service, otherwise known as sheetrock or plasterboard, is the standard wall material used in most modern houses and apartments these days. The main reasons are that it’s affordable, easy to install, and allows you to create seamless, relatively durable wall surfaces throughout living spaces that can be painted, wallpapered, or textured however you prefer with relative ease. But while drywall is flexible and convenient for dividing up rooms, it can still get damaged pretty easily if you aren’t careful. And fixing dents, cracks, holes or water stains in drywall usually means bringing in professionals and rolling up your sleeves for some hassle and expense that could’ve been prevented quite easily. The good news is that there are common sense steps homeowners can take to prevent drywall damage. So here are the biggest tips for guarding your walls and ceilings to minimize damage issues down the road. A little bit of pro activity early on will save you headaches (and cash!) later. Use Corner Guards and Wall Padding One trick of the trade every homeowner should know about preventing drywall damages is the importance of Installing corner guards in high-traffic zones and foam or plastic wall padding as “bumpers” along hallways and entries. Doing so will help cushion inevitable contact from furniture, equipment, people, pets, and any other objects that may bump the walls. This shields vulnerable wall surfaces in a nearly invisible way from the most common dings, cracks, holes, and other signs of wear and tear. A smart and affordable choice that does the preventative work for you by absorbing impact. Keep Walls Dry Water is drywall’s worst enemy. From leaky roofs and pipes to overflowing showers, any excess moisture absorbed into drywall will start comprising its structural strength and integrity. Left alone, drywall water damage leads to bulging, crumbling, and eventually mold issues that require major cut-outs and repairs. So, stay vigilant for wet spots, respond ASAP to any leaks or flooding, and ensure any Skyline Drywall Repair Service near water sources like bathrooms remains properly ventilated to prevent condensation. Catching and resolving moisture sources quickly is key! Baby Those Walls It’s just a reality – walls need babying in family homes or else they get beat up fast. Remind kids not to kick, punch or throw objects at walls which puncture easily. Use appropriate supports and hangers for decor pieces and shelves so the weight doesn’t gradually crush drywall at the anchors. And when moving stuff around like furniture or appliances, avoid scraping and denting walls by padding corners and taking things slow and steady. Basically, handle walls with care as if they were a newborn infant! It’ll pay off for long-term prevention. Regular Inspections Make a habit of doing routine workarounds in all rooms scanning walls and ceilings up close for early signs of damage trouble emerging – cracked corners, bulging shapes, mold, split seams, etc. Issues can develop and worsen gradually over time out of eyesight, so consistent monitoring helps catch stuff before major repair needs set in. Rapid Repairs When Needed Despite best efforts, stuff happens! But the key for homeowners is addressing any drywall dings, holes and deteriorating spots right away before further crumbling occurs. For nail pops, bubbles and holes smaller than a few inches wide, basic patching kits can usually handle things. More serious gashes likely need boards fully replaced – nail in new drywall pieces after cutting back damage to wall studs, tape seams and skim coating for fresh finishes. The Bottom Line While you probably can’t prevent all drywall damage realistically, staying vigilant and proactively protecting vulnerable areas from moisture, traffic, etc will help your walls hold up better in family living spaces long-term. And make repairs swiftly – it saves bigger headaches down the road!
Bathroom Blocking
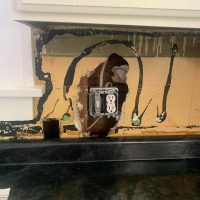
Bathroom Blocking Bathroom Blocking is a topic about planning the bathroom blocks like towel rack, closet shelves and safety bars. This article is an excerpt from the book called “How to build a house” by “Larry Haun” BLOCKING IN BATHROOMS AND CLOSETS Nailed between studs, blocking provides solid backing for items such as towel racks, closet shelves, and safety grabs bars. Blocking ensures that the mounting hardware for those devices can be anchored with screws driven into solid wood, so that you don’t have to worry about racks, bars, and shelves pulling loose. It’s smart to include blocking when marking up wall plates. Cut blocking boards from 2× scraps. Blocking is installed so that the face of the 2× is flush with the edges of the studs. To help locate blocking, use these standard heights for common bath, kitchen, and storage fixtures. Towel bars: Near the tub and vanity, center blocks 54 in. above the floor.Toilet-paper holder: Near the toilet, centre blocks 24 in. above the floor.Toothbrush and soap holder: Above the sink, center blocks 40 in. above the floor.Safety grab bars: Near the toilet and near (or in) the bathtub/shower, center blocks 36 in. above the floor.Closet shelf and pole: Block 66 in. above the floor; more blocking may be needed if you install wire shelves.Linen-Closet shelves: First block above the floor at 20 in., then block every 14 in, thereafter for above-floor measurements of 34 in., 48in, 62in., and 76 in. Don’t forget to block for a shelf or two in the utility room to hold detergent and other laundry items.Kitchen cabinets: Block below 36 in. for base cabinets, above 54 in. and below 84 in. for wall cabinets.Shutters: Block at the top and bottom of windows at least 12 in. wide.
Proper drainage around House
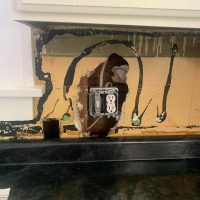
Proper drainage around House This article is an excerpt from the book called “How to build a house” by “Larry Haun”. This gives a guidelines to keep the water away from the foundation. ENSURING PROPER DRAINAGE We need water , We just don’t need it in our basements or under our floors, causing dampness, mold, and rot. We may not be able to hold back the Mississippi when it floods, but we can control most of the rainwater falls around our homes. Follow the guidelines below and you’ll stand a good chance of keeping water on the outside of your foundation. Don’t build on the lowest part of the lot.Seal all holes around the pipes that go through the concrete.Install perforated drainpipes at the bottom of the concrete footings around the outside of the foundation.Coat the foundation walls with a suitable damp-proofing or waterproofing treatment. Check with builders in your area or the local building department to find out which foundation coatings are recommended. Tar coatings are expensive but not as effective as more recently developed waterproofing treatments.Compact loose fill as you backfill around the foundation, but be careful, because excessive compaction can damage masonry walls. Make sure that the finished grade (ground level) slopes away from the foundation. But remember that loose fill can settle. A finished grade that slopes away from the house may later slope toward the house should settling occur.Use gutters and downspouts to manage high roof water runoff. Make sure you keep gutters unclogged and install down spouts to direct water away from the house.Get advice from your building department. The time to protect your house from water infiltration is while you are building. Fixing a leaky basement or a damp crawl space after the house has been built can be very expensive.
Cost of Building Basement
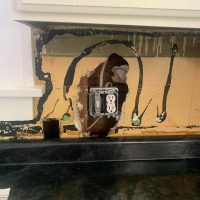
Cost of Building Basement Cost of building a basement could vary based on various factors. This article is an excerpt from the book called “How to build your own TINY HOUSE” by “Roger Marshall”. This helps in estimating the cost of a sample basement project. Please leverage this to calculate your DIY home renovation projects. CALCULATING THE COST OF STRUCTURE 1.If the hose has a slab or basement(let’s say the footprint is 20ft. × 25 ft.), in either case you will lay insulation on top of the wall and place a pressure-treated (PT) 2×8 sill plate all around the edge. That amounts to: 25ft.×2 + 20 ft. ×2, Which comes to 90 ft. of PT 2×8. If you have a basement, you will need two 20 ft.-long beams that will run across the basement and support the floor joists. These beams will be 5 1/8 in., or you can use smaller beams with a single post in the middle of the basement floor.If you have a slab in a warm climate, you can simply tile over the concrete. In a cold climate, you might want to lay a moisture barrier, and then put 2×4s inside the sill plate. You can lay foam insulation between the 2×4s and cover the entire structure with 3/8- in plywood.Separate the floors, walls, and roof. Each wall will be made up of studs, headers, and top and bottom plates. Count the number of studs and the total linear footage of the headers and plates and multiply by the cost per item to come up with a price. Add in the wall covering (such as Tyvek ) and then calculate the total wall area to find out how much sheathing you will need.The floor is made of 10-ft.-long 2×8s resting on the walls and the transverse joists. Count the number of floor joists you will need and price them.The roof should also be priced out by breaking it into its component parts (rafters, joists, sheathing, and roof covering).You will need to add nails or screws, caulking, and possibly glue.Count the exterior door(s) and price each one. Then count the interior doors and price them.Count the windows and price them out.When all is done, add in at least 10% or so. You will usually not busy all the materials at the same time and prices may fluctuate.
Proper drainage around House
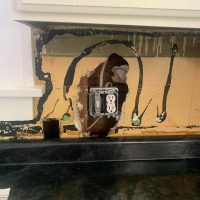
Proper drainage around House This article is an excerpt from the book called “How to build a house” by “Larry Haun”. This gives a guidelines to keep the water away from the foundation. ENSURING PROPER DRAINAGE We need water , We just don’t need it in our basements or under our floors, causing dampness, mold, and rot. We may not be able to hold back the Mississippi when it floods, but we can control most of the rainwater falls around our homes. Follow the guidelines below and you’ll stand a good chance of keeping water on the outside of your foundation. Don’t build on the lowest part of the lot.Seal all holes around the pipes that go through the concrete.Install perforated drainpipes at the bottom of the concrete footings around the outside of the foundation.Coat the foundation walls with a suitable damp-proofing or waterproofing treatment. Check with builders in your area or the local building department to find out which foundation coatings are recommended. Tar coatings are expensive but not as effective as more recently developed waterproofing treatments.Compact loose fill as you backfill around the foundation, but be careful, because excessive compaction can damage masonry walls. Make sure that the finished grade (ground level) slopes away from the foundation. But remember that loose fill can settle. A finished grade that slopes away from the house may later slope toward the house should settling occur.Use gutters and downspouts to manage high roof water runoff. Make sure you keep gutters unclogged and install down spouts to direct water away from the house.Get advice from your building department. The time to protect your house from water infiltration is while you are building. Fixing a leaky basement or a damp crawl space after the house has been built can be very expensive.
Electrical Work
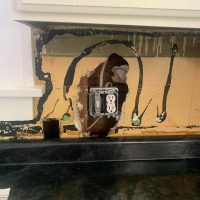
Electrical Work This guide to your DIY home projects, electrical work. This article is an excerpt from the book called “How to build your own TINY HOUSE” by “Roger Marshall”. Please leave a positive comment in the comments section, if you like the articles 10 Pointers To Guide Your Electrical Decisions Use LED lighting throughout to cut down on power usage.Use Energy Star appliances wherever possible.Receptacles can be located at any height comfortable for the design, though typical height is at least 12 in. to 15 in. off the finished floor.If you plan on installing outlet boxes above countertops, they should be 9 in. to 12 in. above the countertop.When locating light fixtures overhead, make sure they are not in a hallway where the fixture might bang heads, but that they properly illuminate the walkway.All outdoor boxes or boxes in wet areas should be waterproof and have a ground fault circuit interrupter (GFCI) breaker or receptacle.Check with your local authority to make sure you are using the correct style of outlet box. Some authorities specify metal only, whereas others allow plastic boxes.Use the appropriately shaped box. Outlets and switches use a 23/4- in. × 4 1/2 in. square box, whereas lighting outlets tend to use 6-in. round boxes in the ceiling. Note that many recessed lighting fixtures come with their own box. You should decide what you need before start the rough wiring installation to avoid multiple trips to the hardware store.Make sure to specify the shortest distance between the outlet box and the main panel and to size the wire suitably for the circuit.If you are planning to run two appliances at the same time- for example, you might run the coffee machine and the toaster at the same time while you have your computer and monitor plugged in- it’s best to put them on different circuits rather than plug them all into one outlet.
Sound Insulation Walls
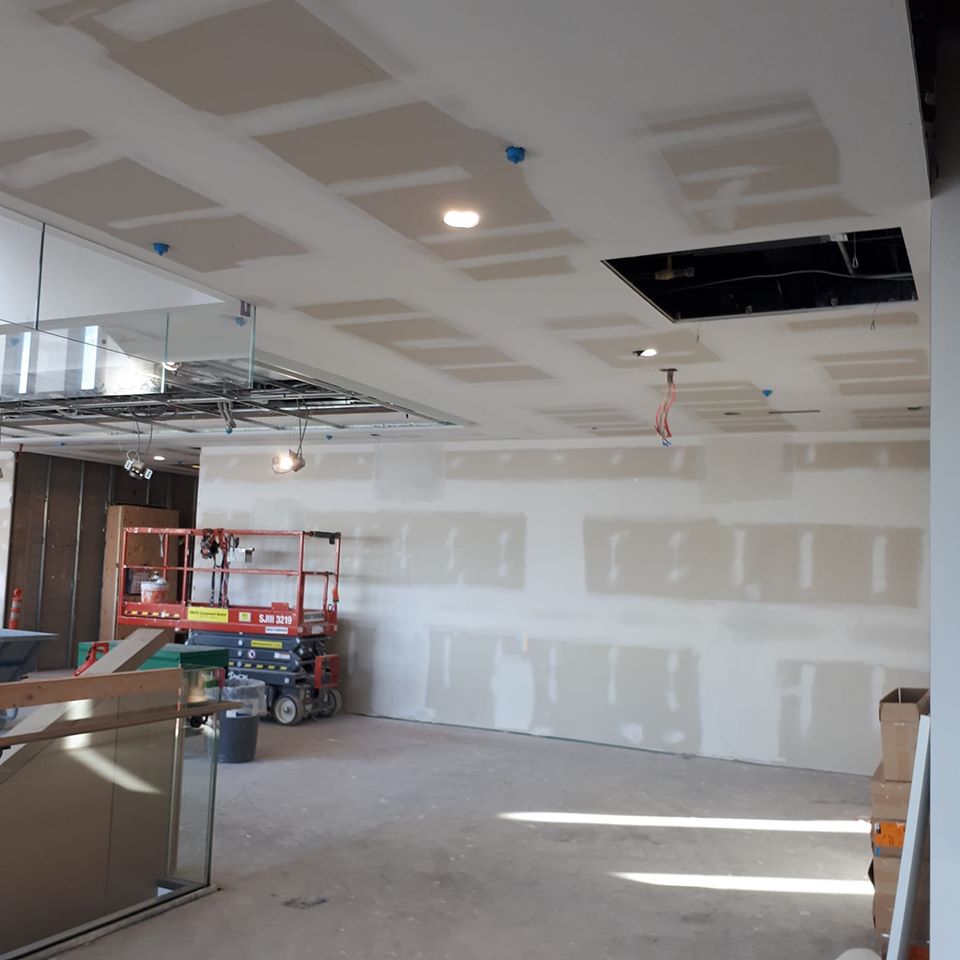
How to create sound insulation walls?. Find answers to your question below. This article is an excerpt from the book called “Stanley Complete DRYWALL” by “Des Moines Iowa”. Thanks to the author. CREATING SOUND CONTROL AND FIREWALLS The irony of successfully decreasing sound transmission is that a room becomes more acoustically reflective. So you’ll probably need to consider adding some sound-absorbing materials such as carpeting and drapes. Consult with your local building officials before building a firewall to ensure that you utilize the correct materials and framing techniques. INSTALL A SOUND-REDUCTION BOARD A special type of wall panel is engineered to serve as the base layer instead of drywall in a two-layer sound-reduction installation.(One brand is Homasote 440 Sound Barrier Panel). Following the manufacturer’s instructions, install the panels vertically to wood or metal studs, using adhesive and screws. Top it with adhesive and No.10×1 ½- inch type G screws driven into the base panel, not the studs. Call Us @ (202) 280-2569 Continue reading about “Demountable Partitions“
Demountable Partitions
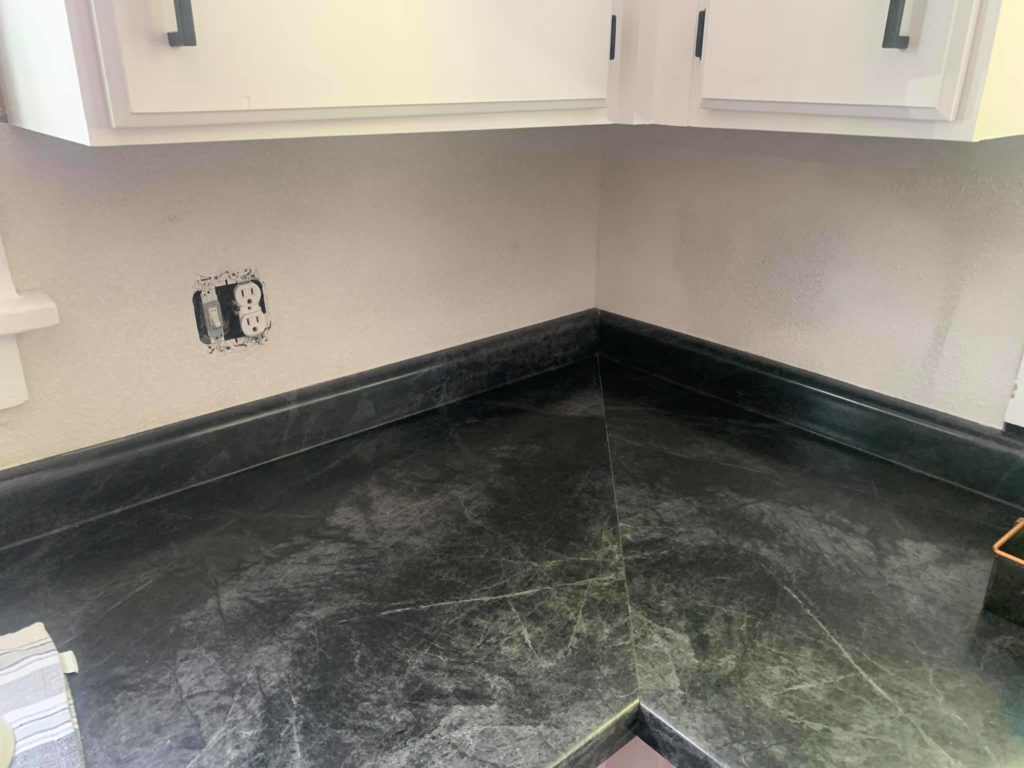
Washington Monument This article is about Demountable Partititons, which is an advanced topic when it comes to drywall projects. This articles in an excerpt from the book called “DRYWALL” by “W Robert Harris”, Please read , thank the author and leave a comment. A demountable partition is a partition designed to be assembled, disassembled, and reassembled in another location with minimal damage to the partition components. Partitions of this type are most commonly used in office buildings where space requirements frequently change. Unlike standard metal stud and drywall partitions, which must be disposed of when removed, demountable partitions can be easily relocated with minimal waste? The salvage rating signifies the percentage of partition components that are reusable when the demountable partition system is relocated. A demountable partition’s salvage rating may be the determining factor when a building owner selects the type to be used. A partition with a high salvage rating may be more expensive initially; however, when the cost of the components destroyed when it is moved from one location to another is factored in, it may cost less. For example, a demountable partition with a high salvage rating that is moved from the third floor to the second floor within the same building will require a minimum number of new components. This reduces the high cost of material delivery and stocking when access is poor. All demountable partitions, regardless of the manufacturer, are designed to divide space. Most utilize tracks or runners at the top and bottom, studs, and drywall sheets or prefinished panels that conceal the framing. Some demountable partitions use clips that hang the panels on the studs. Others require screws for attaching the panels to the studs and rely on battens to cover the screws at the joints. There are progressive systems in which interlocking sandwich panels are started at one side of the room. Additional panels are added as the installation progresses to the opposite end. (202) 280-2569 Washington Monument Regardless of the manufacturer or the type of system used, seven basic rules should be followed when installing demountable partitions: Be sure that the partition layout has been completed before the panels are stocked in the room where they will be installed. Demountable partitions are usually installed in finished rooms and material storage space may be limited. Repeated moving of prefinished panels increases the potential for damage.Double-check the layout before fastening the tracks to the floor. Damaged carpets or floor tile caused by improperly located floor tracks may be impossible to repair.Take all measurements and make all cuts accurately. Most demountable partitions use a top track component that is a finished member with no additional trim at the ceiling. Poorly-fitting corners and track joints are unacceptable and costly to correctInstall all framing members correctly. Accurate layout of the studs is very important since the prefinished panels should not be cut.Handle the panels carefully to avoid damaging the panel faces and edged. The finished appearance of the partition is directly affected by the condition of the panels.Be sure all door and window frames are installed correctly (plumb, true, and securely fastened to the framing).Exercise care when removing unused material or scrap from finished rooms.
Drywall Access Panels
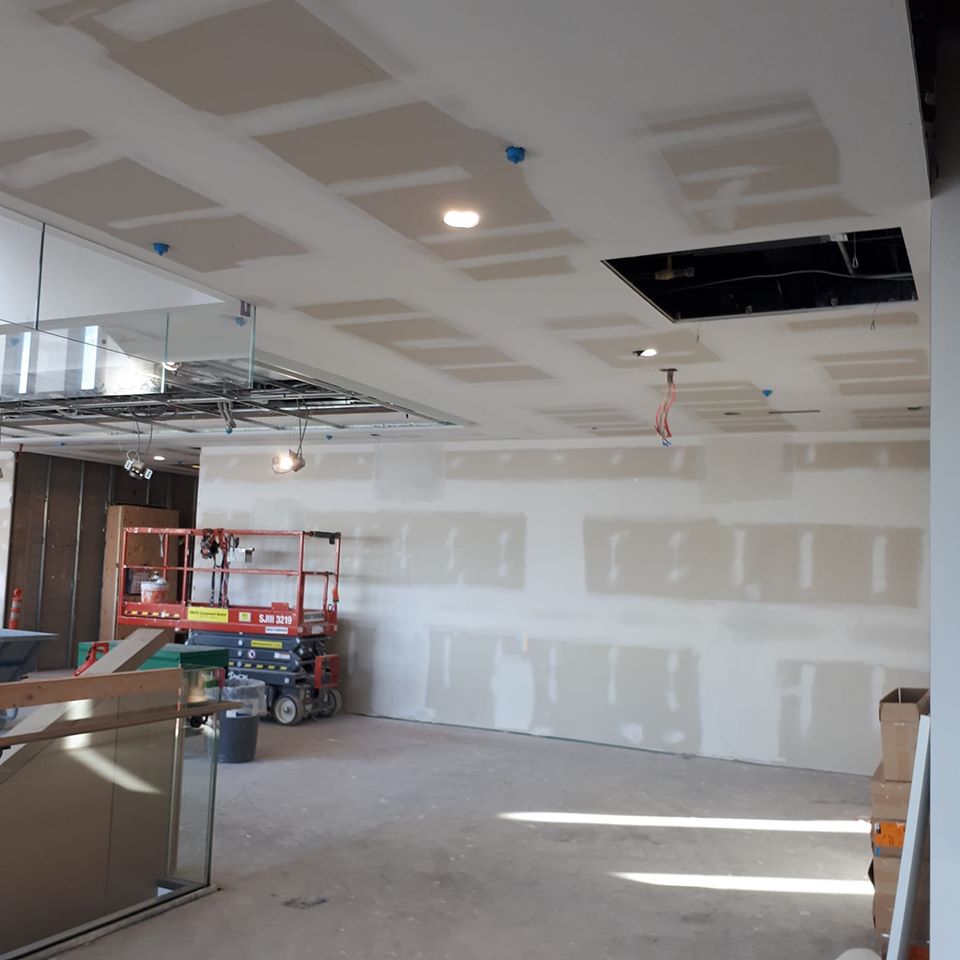
Drywall Access Panels Special Drywall Access Panels listed for the benefit of our readers. this article is an excerpt from the book called “Ultimate Guide DRYWALL” by “John D Wagner” DRYWALL PANELS FOR SPECIAL USES Flexible Drywall: This ¼ – inch –thick material is intended for tighter curved-wall or archway applications and is often applied in two layers. Flexible gypsum drywall has a stronger liner and face paper than regular ¼- inch-thick drywall and resists cracking more effectively. Abuse- Resistant Drywall: Compared with standard gypsum panels, abuse-resistant panels have a heavier paper covering and a reinforced core. These panels give greater resistance and a reinforced core. These panels give greater resistance to damage. Available in ½- and 5/8- inch thicknesses, this stock is recommended for playrooms, high-traffic hallways, and garage and basement walls that are likely to sustain damage from bikes or tools. For this type of usage, manufacturers have recently developed a gypsum/wood fiber backing that resists dents and punctures better than paper and increases panel strength. Stock with this backing costs more than ordinary gypsum drywall and usually must be special-ordered. Moisture-Resistant Drywall: Also called MR (moisture-resistant) board, WR (water-resistant)board, green board, or blue board, this gypsum drywall (which has a pale green or blue face) resist moisture but is not waterproof. It can withstand the high levels of humidity that often occur in bathrooms, kitchens, and laundry rooms. These panels make a good base for any kind of tile attached with a mastic. Avoid hanging the material over an existing vapor barrier, because this would trap moisture, causing the drywall to degrade over time. Moisture- resistant drywall can be finished and painted or wallpapered like regular drywall panels. It should be installed on studs framed 16 inches on center. Cement Board: Also called Cementitious panel, Durock, Hardibacker, Wonder Board, or DensShield, this ½- or 5/8-inch – thick stock comes in 5- or 8- foot lengths and in widths of 32, 36, and 48 inches. Unlike gypsum-based products, this material consists of a Portland cement core sandwiched between layers of a polymer-coated glass fiber mesh. It provides excellent fire and water resistance and makes an ideal backing for tile, especially in high-moisture areas such as bathroom and kitchen walls and floors. It also offers a superior underlayment for use with slate and quarry tile. Each cement- based board has a rough and a smooth side. Install the rough side facing outward when attaching tiles with mortar (such as Quikrete) or with the smooth side out when using adhesive or mastic. Some Cementitious products are UL-listed for use as wall shield and floor protectors in rooms with exposed heaters and wood stoves. Maximum stud spacing for application is 16 inches on center. Fire-Resistant Drywall: Available in ½- and 5/8-inch thickness, this material, known as Firecode Core, Fire-Shield, Fireguard, or Fi-Rock, is fire resistant. This means that it meets or exceeds the ASTM C36 rating for Type X fire-resistant gypsum board, which specifies that glass fibers be embedded in its core, enabling it to resist fire for a certain amount of time beyond conventional gypsum drywall. Typically, a ½-inch-thick panel is rated to contain a fire for 45 minutes, a 5/8-inch-thick panel for 60 minutes. Codes often require these panels for party walls (between condos or apartments), for ceilings that adjoin other units, and for rooms that are susceptible to fire, such as furnace rooms, attached garages, and kitchens. Foil-Backed Board: Where a vapor barrier is required, foil-backed panels may be useful. His stock is made by laminating aluminum foil (backed by Kraft paper) to the surface of a gypsum drywall panel. The foil face increases the insulation value of the drywall and helps create a vapor barrier if the foil face is placed against the studs on the interior side of exterior walls. As with any vapor barrier, this helps prevent moisture in the living area from entering the stud bays. Avoid using foil-backed panels as a base for tiles or in any area where another wall covering could trap moisture within the core of the panel. Also, avoid using this material in air-conditioned structures that ordinarily withstand frequent high outdoor temperatures and humidity.
Drywall Sanding Corners
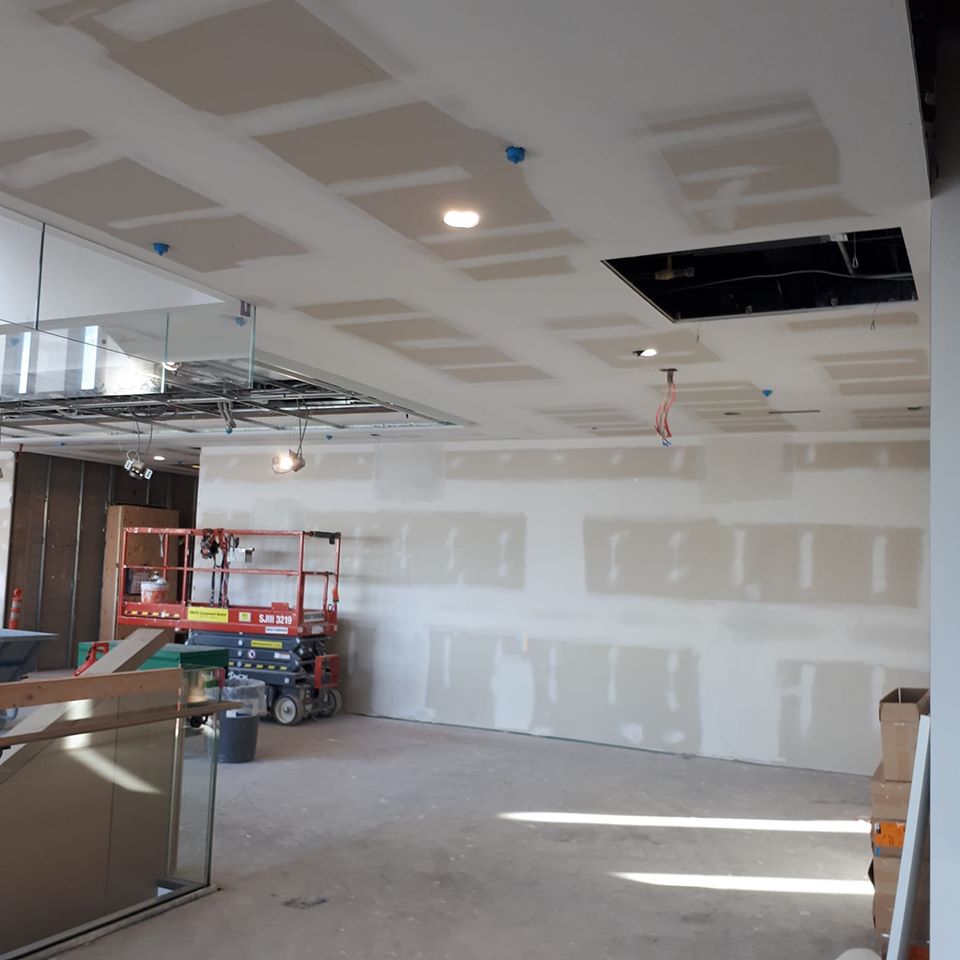
Drywall Sanding Corners This article is an snippet from the book called “Drywall Taping” – Workbook. This article gives a detailed description about drywall sanding corners. Sanding, like any other operation in the taping trade, can be made difficult or it can be a relatively easy part of the work. When a worker uses the proper tools, the correct type paper, and has an understanding of what he is trying to accomplish, the necessity for sanding is minimized and such sanding as is required is simplified. Sanding Pressure It is not necessary to apply heavy pressure when hand sanding or using a sanding pole. The sanding block and sandpaper should do the work. With the correct sandpaper (the most commonly used is 80 0r 100 grit),a taper can do the necessary sanding without it becoming a difficult or tedious chore. Finish Compounds A prime factor in making sanding easier is in having used reasonably soft finishing compounds when taping the job. The proper selection of finishing compounds can save time and work with the sanding operation. If bedding cement is used for final coats rather than finishing compound, the sanding process is made twice as difficult. This is because bedding compound, when set up, presents a relatively hard surface and is not so readily sandable. Preparation and Sanding When the joints are run correctly with the finishing tools and checked prior to sanding by hand, the result will be a smooth finish that needs very little sanding. The edges of the finished joints and fastener covering should be sanded lightly to eliminate any rough edges. Some shops use a sponge and water to smooth edges. This like sanding, is a skill acquired by practice and “feel.” If the joint is wiped too hard and too much water is used, the feathered edge will not remain smooth. The same is true when using sandpaper. Excessive sanding will not only change the feathered edge but will also raise the nap of the face paper, causing difficulty for the painter. If excessive sanding is required, the application of the joint cement and/or finishing compound was incorrectly accomplished. “Touch-up” and Second Coat Sanding The touching-up process is a very vital part of sanding to obtain an ultimately smooth surface. Any scratch lines, recesses, or imperfections should be marked or remembered when sanding. After being sanded, some areas will always need an additional hand application of joint compound. A light sanding between the second and third coats is very helpful and necessary. It shortens the time consumed I n the final sanding by creating a smooth surface for the finish coat or coats. TAPING APPLICATION THIRD COAT-SKIMMING This topic, “Third Coat-Skimming,” is planned to provide answers to the following questions: The third coat of compound over the taped joints and butt joints is applied after the second coat is dry. A light sanding of any burns or splattered joint compound or other material that may have gotten on the surface of the wallboard is necessary to eliminate scratches or chatters in the finished third coat.Third Coating The constiency of joint compound for the third coat is similar to the thickness of the material used for the second coat. It is thick enough to be workable with tools and thin enough to apply only the necessary thin finishing coat to the joint. This coat will extend as need beyond the edge of the second coat, which may vary from 7 to 10 inches wide on recessed seams or joints and 15 to 20 inches on butt joints. All excess compound remaining at laps, at a crossing, or at an intersecting joint should be wind smooth so that little or no extra work will be required. After all the joints have been coated, it may be necessary to recoat a remaining joint that is hollow or sunk. An extra few minutes will make the job more complete and save time in the next step preparation of the finishing job. Corner Finishing by Machine Corner finishing is accomplished quickly and easily with the Ames corner finisher by using a thinner joint cement than is used in the second or third coating. After ensuring that the inside corners are dry and sanded to remove any ridges or splattering of joint compound or other material, the corner finisher is placed at the top of a vertical corner and the finisher blades depressed so as to produce a smooth feathered edge finish. The tool is then guided downward, maintaining pressure at the center of the corner. When the tool is as close to the bottom of the corner as the operator can reasonably maneuver it, for instance one foot from the end, The pressure is released and the tool is turned in the hand to permit an upward stroke similar to the downward stroke. The corner finisher is then placed in the horizontal angle of the intersecting ceiling and wall angles. A similar pressing in of the corner finisher, along with walking forward-with the pressure of the tool being directed to the center of the corner or angle-results in filling the shrinkage and at the same time feathering the edges. When a certain number of angles are run in this manner, depending on drying conditions, wiping-in will begin. This consists of pointing-up or wiping-in each area and making a neat square corner. This may be done with a 6-inch broad knife or a 7-inch wipe-down knife. Care must be taken to keep the corner finisher tool clean and undamaged so that it will produce good, clean trouble-free work. Dropping the corner finisher may break the finishing blades, which will then have to be repaired.